glass beads for blasting
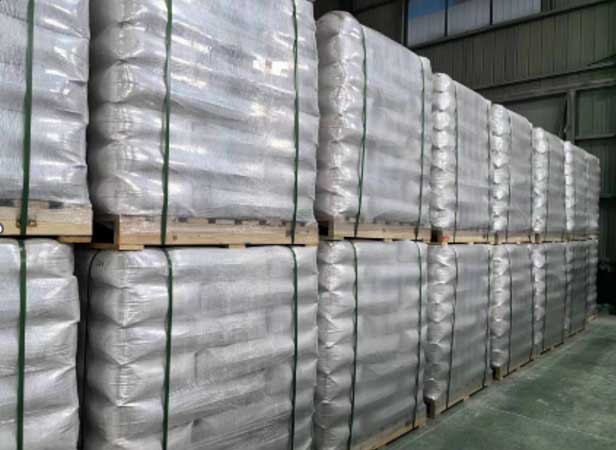
Glass beads for blasting :Using glass beads for sandblasting, also known as sandblasting abrasives or sandblasting glass beads, is essentially a method employing glass beads for sandblasting processes. Throughout the application process, the primary goal of using glass beads for sandblasting is to remove burrs and clean the surface of objects.
What Are Bead Blasting’s Applications?
Aerospace industry | Remove rust and paint from mechanical components to remove knife marks. |
Remove scratches on the rubber | Reflective paint for roads |
Scratch treatment on the surface of stainless steel. | |
Foundry industry; | Pre processing in the electroplating industry. |
Semiconductor Industry | Crafts for exterior decoration |
glass beads for blasting
This is particularly effective on metal and stainless steel surfaces, as well as softer decorative surfaces, to remove blemishes, burrs, and achieve a matte finish.
Glass beads for blasting can clean molds to extend their fatigue life and is also effective in removing burrs from semiconductor devices, metal pipes, and various metal components.
These non-toxic and environmentally safe glass microbeads can be safely reused, promoting sustainability and reducing resource waste. Due to their low toxicity, they are harmless to humans, meeting safety and environmental requirements compared to equivalent products.
Because the main component of glass used for sandblasting is glass itself, it possesses high transparency.
It typically achieves sandblasting effects by impacting and wearing the surface of objects while maintaining their original transparency. The uniformity of glass microbeads is highly recognized.
After surface treatment, the sandblasting effect becomes more uniform. The spherical shape of glass beads used for sandblasting ensures even distribution of impact force, reducing damage to workpieces.
Their high chemical stability, especially for materials sensitive to chemical properties, ensures they do not react with other chemical substances.
When using glass microbeads for sandblasting, appropriate protective equipment should be worn to ensure the safety of operators. Glass microbeads have become an indispensable material for sandblasting in many industries. Selecting the appropriate size of glass microbeads is crucial as it directly impacts the final surface treatment effect and helps avoid damage to some workpieces.
The chosen size varies depending on the degree of surface treatment required, making it a critical factor. Another advantage of sandblasting with glass microbeads is its ability to enhance the fatigue resistance and corrosion resistance of components.
Size of glass beads for blasting
Model of Bead blasting glass | Sieve Size (mesh) | Particle Size Range(μm) |
WSL17L# | 20~40 | 425 ~ 850 |
WSL 18L# | 30~40 | 425 ~ 600 |
WSL 19L# | 40~60 | 300 ~ 425 |
WSL 20L# | 60~100 | 150 ~ 300 |
WSL 21L# | 70~140 | 106 ~ 212 |
WSL 22L# | 100~140 | 106 ~ 150 |
WSL 23L# | 100~200 | 75 ~ 150 |
WSL 24L# | 140~200 | 75 ~ 106 |
WSL 25L# | 140~270 | 53 ~ 106 |
WSL 26L# | 200~325 | 45 ~ 75 |
Specification of Bead blasting glass
Specific gravity | 2.4-2.6 g/m3 |
Stacking density | 1.5g/cm3 |
Type | Blasting / Shot Peening Media |
Spherical | |
Rockwell hardness: | 46HRC |
Mohs | 6-7 |
Round rate | 80% |
Melting point | 710-730 ℃ |
Index of refraction | 1.5—1.6 |
After glass bead sandblasting, various types of surface textures can be produced, primarily including the following types:
1. Rough texture: Produced by using glass microbeads, the surface usually exhibits a noticeable graininess. This type is typically used before coating to improve surface adhesion, often with larger diameter glass microbeads, enhancing friction, anti-slip properties, and providing better adhesion.
2. Semi-matte texture: This is a soft surface effect between matte and glossy. It is usually applied in softer decorative areas. In such cases, using medium-sized glass microbeads can achieve a good semi-matte effect.
3. Smooth surface effect: Unlike semi-matte effects, this surface effect has more gloss. It is generally used on optical components’ surfaces. We recommend using smaller diameter glass microbeads and lower sandblasting pressure to achieve a smooth surface effect. It simultaneously removes burrs and improves the appearance quality.
4. Uniform etch effect: After using medium-sized glass microbeads, the surface appears to have a regular texture due to grinding. This texture is typically used in electroplating processes to achieve a uniform etch effect.
5. Matte effect: Using smaller-sized glass microbeads can achieve a matte effect, characterized by very weak gloss. This is often used on medical devices and stainless steel surfaces to reduce light reflection.
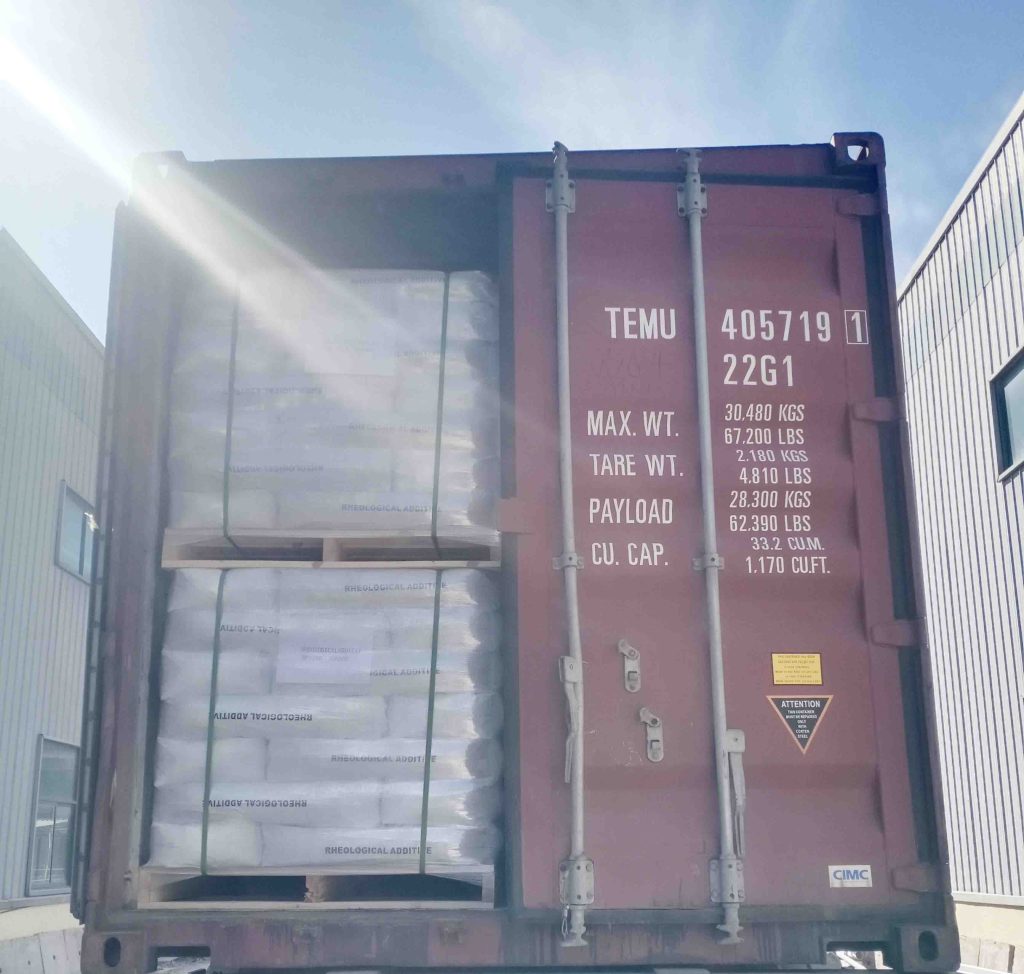
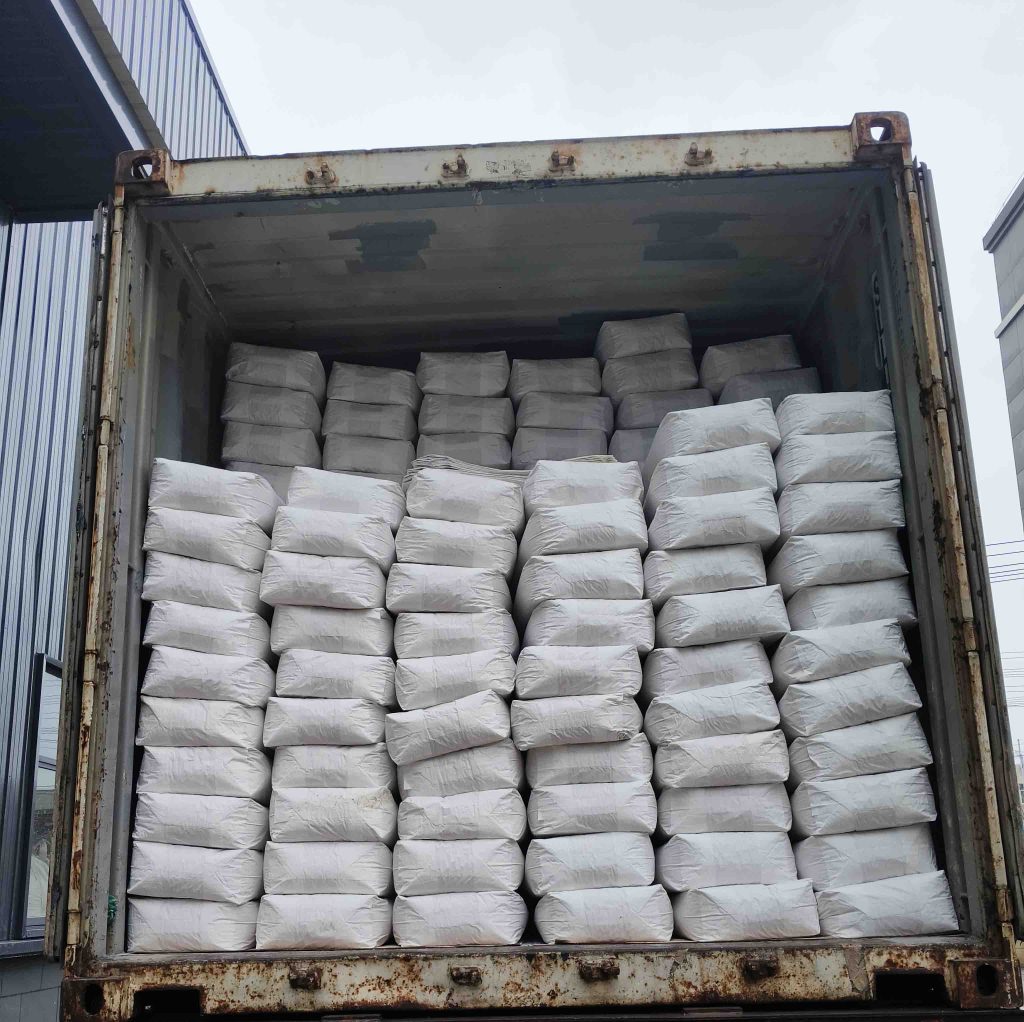
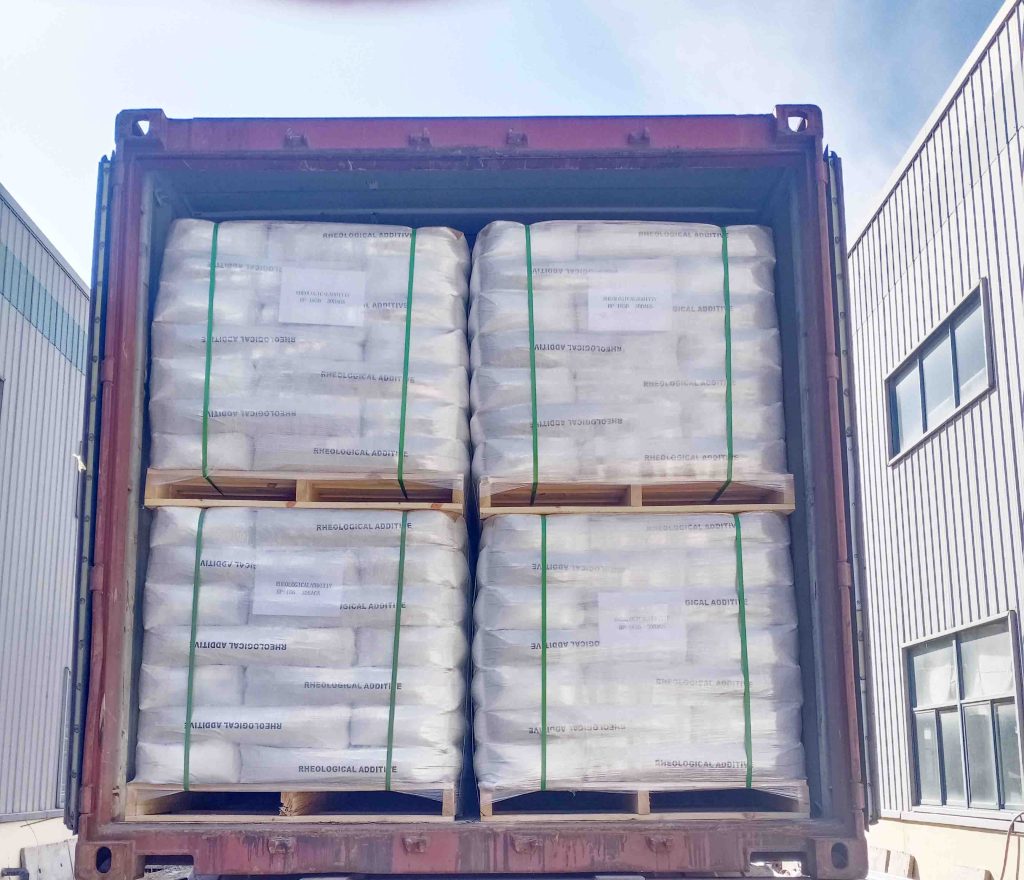